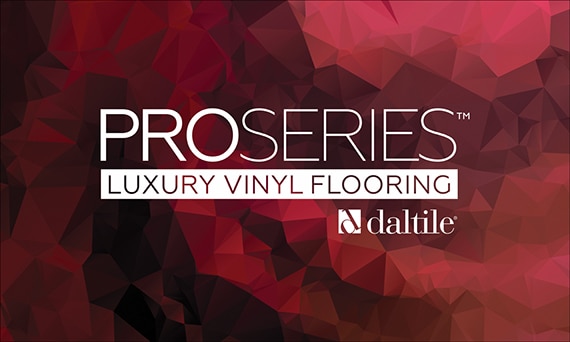
HOW TO INSTALL PROSERIES
Daltile ProSeries resilient/LVF (luxury vinyl flooring) is recommended for a variety of commercial applications, including educational, institutional, healthcare, retail, office, hospitality and multifamily environments. ProSeries may be installed over most properly prepared substrates, making it suitable for installation on all grade levels where moisture conditions do not exist.
Download the installation guide for your ProSeries flooring.
INSTALLATION GUIDES
Additional Resources
Discover LVF
When Daltile, the tile industry's leader, produces luxury vinyl tile, you know it's high-quality.
Trade Pro
Resources
Explore programs, products, and other resources developed with Trade Pros in mind.
Got Questions?
We have answers. We're here to provide information on our company, services & products.